Compression Molding
PROCESS OVERVIEW:
Closed mold injection or matched die processes are widely used to produce three-dimensional products in composites manufacturing. Injection molding advantages include short cycle times, higher volumes and handling automation. Glass surfacing veils, fabrics and reinforcements are placed into the mold cavity before the top is closed. Resin is then injected under high pressure. Part cooling takes place while the material is under high pressure, resulting in shorter cycle times. SI Veils enhance part finish and surface appearance in this process.
SI Veil Design Considerations:
When selecting the proper SI Veil, the designer should consider several areas
Veil Thickness / Weight:
Final design should be determined after sample part testing. Typical SI Veils frequently used will range between 10 mil and 20 mil thick.
Width:
When specifying veil width, consider the overall part design, including the part wall depth. SI Veils may be specified up to 120 inches (3.048 m) wide.
Fiber Orientation:
- Pearlveil® is typically used for relatively flat molded parts
- Curveil® is designed for moderate to highly curved molding
- Flexiveil® is used for compound curved molding applications
Fiber Wash:
The veil must be capable of maintaining its placement in the mold during high injection pressures, thus eliminating fiber wash.
- Series 100 Binder is more soluble and more conformable to complex shapes.
- Series 200 Binder offers more strength and resistance to fiber wash at higher pressures.
- Other: consult Factory.
Binder Percentage:
Binder percentage can be specified on all SI Veils, ranging from between 7% and 15%.
Resin Flow-ability:
The veil must enhance resin flow during the injection process. SI Veils have an open construction to enhance wicking and eliminate air entrapment.
Smoke and Fire Suppression:
All SI Veils consist of glass mineral fibers that are non-toxic and do not burn.
Post Mold Finishing:
SI Veils offers many advantages to post mold finishing, among others are:
- The translucent color allows for enhanced resin pigmentation or post painting
- Parts can be sanded before post painting
- The glass fibers shear cleanly when holds are punched into the part
PACKAGING:
SI Veils are attached and wound onto a heavy duty 4-inch I.D. cardboard core, immediately sealed against contamination in a polyethylene bag and identified with a unique product specific label.
Based upon quantities, SI Veils are usually shipped on a 45 inch x 45 inch wooden pallet. Optional packaging is available.
STORAGE:
For best performance, all veils should be stored upright in locations with temperatures between 50° F (10° C) and 85° F (30°C) with a relative humidity below 80%.
QUALTIY:
All SI Veil products are produced in the United States and meet the demanding quality requirements within the industry.
WARRANTY : See Schmelzer Industries Product Warranty.
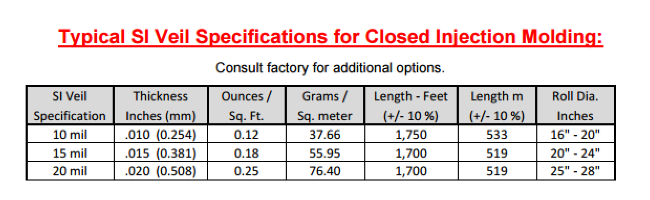